Common Myths About Steel Frame House Extensions
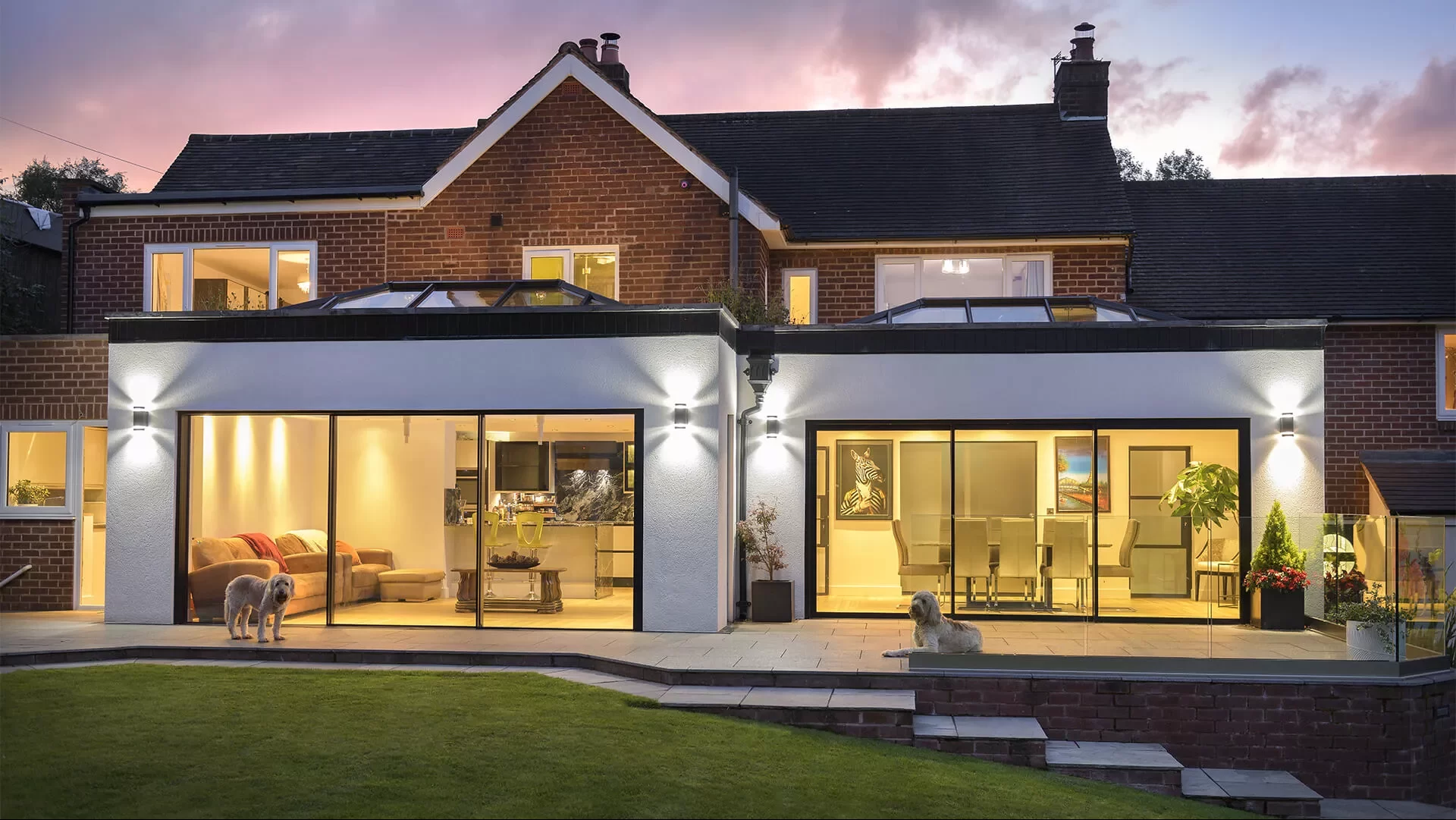
Steel frame house extensions are becoming increasingly popular due to their durability, flexibility, and speed of construction. However, despite their many benefits, there are still several misconceptions that can deter homeowners from considering this innovative building method. In this article, we’ll address and dispel some of the most common myths about steel frame house extensions, backed by technical insights and real-world experience.
Myth 1: You won’t be able to get a property with a steel frame extension mortgaged because it’s classed as non-standard construction
One of the most persistent myths is that properties with steel frame extensions are considered non-standard construction, making it difficult to secure a mortgage. This is not the case. As long as the steel frame extension meets building control standards and is fully signed off by the local authority or an approved inspector, obtaining a mortgage is no different than it would be for a traditional build.
The key to mortgage approval lies in compliance with building regulations. Building control certification ensures that the extension has been built to meet stringent standards for safety, longevity, and performance. Modern steel frame extensions are robust and structurally sound and have undergone rigorous testing to prove their durability and compliance. Many mortgage lenders recognize this, especially with advances in construction technology that make steel frames as reliable as, if not more so than, timber or brick builds.
Cold bridging occurs when there is a break in the insulation, allowing heat to escape and cold to enter, which can lead to energy inefficiency and condensation issues. This myth stems from the misconception that steel, being a conductor of heat, is prone to cold bridging. While it’s true that steel can conduct heat, this issue only arises when the extension is built incorrectly.
At Xtra Space, we use a warm frame system that mitigates cold bridging entirely. A warm frame design involves placing the insulation outside the structural steel, ensuring that there is a continuous thermal barrier around the building. This method eliminates direct contact between the steel and the external environment, meaning the steel is insulated and does not become a thermal bridge. As a result, steel frame extensions can achieve thermal performance values that are equal to or even better than traditional builds, all while requiring smaller wall cavities.
By using high-performance insulation materials and correctly sealing the junctions between different building components, we ensure that our steel frame extensions meet or exceed current energy efficiency standards, keeping your home warm and reducing energy bills.
Myth 3: Your insurance premiums will go up if you opt for a steel frame extension
Another common misconception is that opting for a steel frame extension will automatically increase your home insurance premiums. However, there is no evidence to suggest that steel frame extensions result in higher insurance costs. In fact, many insurance companies view steel as a favorable material due to its resistance to common issues like fire, rot, and termite damage—factors that can lead to higher premiums in traditional timber constructions.
Having completed over 100 steel frame projects, we have yet to encounter a client who reported an increase in their home insurance premiums due to their extension. As long as the extension complies with building regulations and is properly insured as part of the overall property, there should be no significant difference in premiums compared to other types of construction.
Myth 4: You are restricted in terms of design with steel frame extensions
Some people believe that steel frame extensions are limited in design flexibility, with rigid or industrial-style aesthetics. This couldn’t be further from the truth. Steel is one of the most versatile building materials available, offering a level of design freedom that traditional materials simply cannot match.
At Xtra Space, we have yet to come across a traditionally designed extension that we couldn’t replicate using our steel frame system. Whether you’re looking for a sleek, modern aesthetic with large open-plan spaces, or you want to match the style of a more traditional home, steel frames can be adapted to suit any architectural design. Steel’s inherent strength allows for larger spans and fewer load-bearing walls, meaning you can create bigger, open spaces with minimal structural limitations.
Additionally, if you already have architectural plans drawn up, we can easily convert them to our steel system structural drawings at no extra charge. This ensures that you get the extension you want without compromising on design or function.
Myth 5: Steel frame extensions have a short lifespan, similar to a conservatory
This myth likely arises from the fact that some conservatories, often built using less durable materials like uPVC, have relatively short lifespans due to issues with weathering and structural integrity. However, steel frame extensions are a completely different story.
Steel is one of the strongest and most durable materials used in construction, capable of withstanding the test of time. The galvanization process, which involves coating the steel with a protective layer of zinc, adds to its longevity by preventing rust and corrosion. Properly galvanized steel can last well over 100 years, far outlasting most traditional construction materials.
In fact, many modern skyscrapers and large infrastructure projects are built using steel frames for this very reason—its unmatched durability and strength. When maintained properly, a steel frame extension will serve your home for generations, without the wear and tear that might affect timber or brick constructions.
Myth 6: Steel frame extensions are noisy during temperature changes
Some homeowners worry that steel, being a metal, will expand and contract with temperature changes, causing noise such as creaking or popping. While it’s true that steel, like all materials, expands and contracts with temperature fluctuations, modern steel frame systems are designed with this in mind.
At Xtra Space, we use advanced construction techniques that incorporate flexible joints and proper insulation to absorb any movement caused by temperature changes. This eliminates any risk of noise, ensuring that your extension is as quiet as a traditional build. Additionally, with proper thermal insulation and design, any temperature-related expansion is minimized, making it a non-issue for homeowners.
Myth 7: Steel frames are prone to rusting over time
While steel is vulnerable to rust in its untreated form, modern construction methods address this concern through galvanization and protective coatings. The steel used in extensions is typically galvanized, meaning it’s coated with a layer of zinc that protects the metal from moisture and prevents rusting. This process significantly extends the lifespan of the steel, making it highly resistant to corrosion.
Conclusion
Steel frame house extensions are a modern, efficient, and durable choice for homeowners looking to expand their living space. While there are several myths surrounding steel frame construction, the reality is that these extensions are just as mortgageable, energy-efficient, and flexible as traditional builds—if not more so. They also come with the added benefits of being highly durable, resistant to many common building issues, and adaptable to virtually any design.
By choosing a steel frame extension, you’re not only investing in the future of your home but also embracing a construction method that offers unparalleled strength and sustainability. Don't let these myths hold you back from experiencing the benefits of a steel frame extension for yourself.
T: 01379 440909